
LIGHT CONVEYOR TECHNOLOGY
INNOVATIVE SOLUTIONS FOR PRODUCTION AND SHIPPING
Wherever it is important to make production and shipping processes efficient and economical, components and systems from AMI light conveyor technology are the right choice / expedient. With the special conveyor technology for light goods - transported in containers or boxes - intralogistics processes can be optimized in almost all sectors, for example in mechanical engineering, in the automotive industry, in medical technology, in pharmaceutical trade as well as in e-commerce and in the paper and plastics industry .
Like all conveyor systems and plants from AMI, the light conveyor technology is also based on a sophisticated modular system of components, modules and
intelligent control systems and a wide range of standardized accessories.
With a service package tailored to the respective requirements, the AMI experts ensure professional, rapid and targeted project implementation for both standard systems and individual conveyor systems. The range of services extends from consulting and planning through design and manufacture to assembly and commissioning. The comprehensive AMI service and maintenance offer ensures the highest level of system availability, 365 days a year, around the clock.
AUTOMATION MATERIALFLUSS INTRALOGISTIK

When it comes to the quality of its extensive range of meat products, Hülshorst Feinkost GmbH, Harsewinkel, is committed to the highest standards - also in terms of sustainability. The production facility, which was redesigned as part of extensive construction work, is supported by a fully automated final packaging line from AMI Förder- und Lagertechnik GmbH, which meets sustainability requirements and offers maximum system efficiency.
When Hülshorst Feinkost GmbH decided to place a stronger focus on automation and sustainability, this involved extensive construction and conversion measures as well as the concentration of two sites down to just the one in Harsewinkel and was also the largest investment project in the company's history. Founded in 1989 by Hubert Hülshorst, initially as a pork cutting plant, the company now produces a wide variety of meat convenience products. Whether meatballs, schnitzel, burgers, pan-fried gyros, gyro skewers, cevapcici, minced meat, roasts or roulades, there is something for every taste. "Our customers," says Christoph Hülshorst (Image 1, left), Managing Director of Hülshorst Feinkost GmbH, "including bulk consumers, system catering and the snack sector, appreciate our wide range of traditional, local cuisine and international specialties and their quality".
As this constantly growing range, in conjunction with increasing customer requirements, also places demands on efficient and sustainable production, the managing directors, Christoph and Philipp Hülshorst, decided to carry out extensive construction and modernization measures. In addition to concentrating on just the Harsewinkel site, the aim was to place an even greater emphasis on sustainability and automation, both in the new building and in the modernization and redesign of production. As a result, these measures required the construction of a new building complex including new production lines for the entire Hülshorst range and their connection to an equally new final packaging facility as well as a heavy-duty conveyor system for transporting pallets ready for dispatch to the new deep-freeze warehouse.
Achieving the goal through active partnership
In its search for a suitable partner to implement the automated end-of-line packaging line, Hülshorst became aware of AMI Förder- und Lagertechnik GmbH and contacted the intralogistics specialist. The Hülshorst management was already impressed by the partnership-based, fast and technically convincing approach to the formulated idea during the first talks. "The initial planning," summarizes Sven Jesberg, Sales Manager at AMI Förder- und Lagertechnik GmbH, "was followed by the award of the contract to us."
This was also the starting signal for the final planning, project management and implementation of a fully automated end-of-line packaging line with upstream carton sealers, subsequent labeling and associated conveyor technology, including for transport to the connected deep-freeze warehouse.
The overall aim behind the construction and modernization project was to make the company's operations even more environmentally conscious, resource-friendly and sustainable. For example, the new building, built to KFW 55 standard, uses the latest energy-efficient technology throughout and its primary energy consumption and CO₂ emissions are only 55% of the legal requirement.

A floor conveyor transports the containers from the level of production line 1 to the first floor
Good planning is the basis
Sustainability and efficiency were also the focus when it came to planning and implementing production, material flow and final packaging. "As our processes were previously largely manual, it was our declared aim to focus more on automated processes," explains Christoph Hülshorst.
This applies both to production and the associated four new lines for the respective meat convenience items, as well as to the final packaging area and the conveyor technology for transport to the new deep-freeze warehouse.
In this context, fully automated final packaging plays a key role in the overall efficiency of intralogistics. Here, the cartons coming from the respective production lines and filled with products from the Hülshorst range are sealed, labeled and palletized by two 5-axis robots. The pallet is then stretch wrapped and transported to the new deep-freeze warehouse using heavy-duty conveyor technology. In order to be able to produce this portfolio of mostly cooked meat convenience products, from schnitzel to meatballs and gyros specialties, both in terms of top quality, efficient material flow and sustainability, it quickly becomes clear that the production, intralogistics and packaging areas play a key role.
The transfer point from production, i.e. from the four production lines to the automatic final packaging area, are the carton sealers, one of which is installed on each line. At the transfer point, the cartons filled with Hülshorst's meat convenience products are sealed on the top and bottom by the carton sealers. The respective carton then runs over an inclined roller conveyor, where it is aligned with a reference edge and then automatically labeled from the side as it passes through.
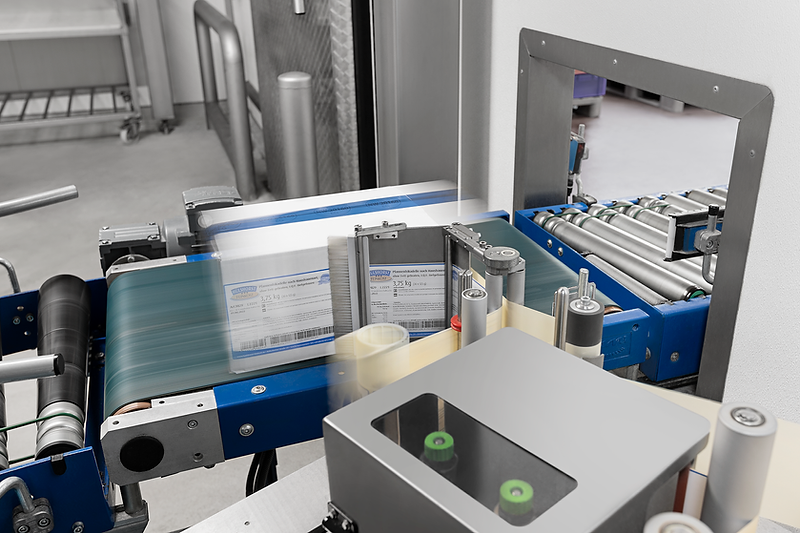
Last station before robot palletizing. A fully packed carton is automatically labeled as it passes through
Automated end-of-line packaging closes the efficiency loop
The connection of the production lines to the automated final packaging and the associated sub-processes was designed by the AMI experts to ensure the highest possible capacity utilization and system efficiency. This results in a consistent sequence for the material flow. Items from production lines 2 (meatballs), 3 and 4 (e.g. gyros) are transported from the first floor via lifts to the upper floor, where product line 1 (schnitzel) is located. Via these four lines, the cartons filled with the respective convenience items reach the automated final packaging area and thus the two 5-axis robots. Prior to this, the empty pallets are destacked and automatically fed to the robots.
Before arriving at the robots, the cartons are scanned and the control system decides which carton is to be palletized by which robot. To do this, the cartons are sorted and ejected onto four stitches (two per robot) by a belt stroke transfer. The cartons are always aligned in pairs at a reference edge. The robot picks up two cartons at the same time and places them on the pallet according to the layer pattern. After a layer has been formed, the robot places intermediate layers. 1083 packs are palletized per hour.
After palletizing and straightening, the pallets ready for dispatch are transferred to the heavy-duty section via chain transfer units and then to the deep-freeze warehouse, from where they are sent on their way to the customer.

Everything here is fully automated. Robot palletizing with subsequent automatic stretching machine (right)
Conclusion
If we summarize the new construction and conversion project at Feinkost Hülshorst in a nutshell, it is clear that the goals set in terms of sustainability and automation have been achieved in full. The automated final packaging line, which ensures systematic palletizing by robot and thus significantly supports the overall efficiency of production and intralogistics, played an important role in this.

Geschäftsführer Christoph Hülshorst (links) und AMI Manager Sven Jesberg stimmen die Feinplanung der automatisierten Endverpackungslinie ab