
LIGHT CONVEYOR TECHNOLOGY
INNOVATIVE SOLUTIONS FOR PRODUCTION AND SHIPPING
Wherever it is important to make production and shipping processes efficient and economical, components and systems from AMI light conveyor technology are the right choice / expedient. With the special conveyor technology for light goods - transported in containers or boxes - intralogistics processes can be optimized in almost all sectors, for example in mechanical engineering, in the automotive industry, in medical technology, in pharmaceutical trade as well as in e-commerce and in the paper and plastics industry .
Like all conveyor systems and plants from AMI, the light conveyor technology is also based on a sophisticated modular system of components, modules and
intelligent control systems and a wide range of standardized accessories.
With a service package tailored to the respective requirements, the AMI experts ensure professional, rapid and targeted project implementation for both standard systems and individual conveyor systems. The range of services extends from consulting and planning through design and manufacture to assembly and commissioning. The comprehensive AMI service and maintenance offer ensures the highest level of system availability, 365 days a year, around the clock.
AUTOMATION MATERIALFLUSS INTRALOGISTIK
USER REPORT:
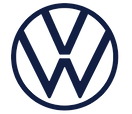
Automated AMI conveyor system optimized
Assembly processes at VW

As part of productivity workshops, the VW automotive group put the processes in the car assembly lines at the Wolfsburg site to the test. One of the results of these workshops revealed the need for action in the positioning area for rear and front bumpers on assembly line 4 in hall 8. The manual handling of the bumper frames delivered by tugger train, which had been practiced until then, was not only time-consuming, but also a feat of strength for the employees. An electrically driven conveyor system from AMI Förder- und Lagertechnik GmbH, Luckenbach, now provides a remedy.
Tugger trains are an integral part of material flow technology in automotive production. This is also the case at Volkswagen AG's largest site in Wolfsburg. The tugger trains are used there to supply the assembly lines with rear and front bumpers "just in sequence", among other things. Steel transport racks measuring 2.4 x 1.5 x 1.5 m (L x W x H) are used as load carriers, each with space for four rear and four front bumpers. "In the past, colleagues had to push the loaded racks from the trolleys of the tugger train on the assembly line into storage bays," recalls Denis Erhardt, Logistics Planner at the Wolfsburg plant (PWL-P/B) of Volkswagen Aktiengesellschaft. "A physically demanding job. Especially when you consider that assembly sets the pace: The workers on the assembly line need a new rack every four minutes."
A productivity workshop revealed the potential for optimization in this area. Erhardt: "The results of the workshop led to a significant streamlining of the processes. This in turn resulted from a reduction in the walking distances for the workers through the use of conveyor technology. In addition, the conveyor technology makes the transfer of transport racks much more ergonomic."
Efficiency created in a limited space
As is generally the case when integrating conveyor and storage technology systems into existing buildings with a fixed material flow layout, the space and time available for the conveyor technology was also limited in this case. During the production-free period between 2019 and 2020, the AMI technicians therefore set up two mirrored conveyor systems for rear and front bumpers in the assembly area on assembly line 4 in hall 8 on an area measuring 14.7 by 5.4 meters. "The technological backbone of the systems are individually manufactured components based on our standard range in the heavy-duty conveyor segment," says Sven Jesberg (photo, right), Sales Manager at AMI Förder- und Lagertechnik GmbH, Luckenbach.
VW Logistics employees feed the racks into the conveyor system by manually pushing the loaded racks from the transport trolley at right angles to the direction of travel onto a feed conveyor. To ensure a smooth transfer, two rails were placed on the hall floor to ensure that the transport trolleys are positioned exactly in the longitudinal direction. AMI has also installed a signal light column on the head frame of the conveyor system, which is activated when a tugger train arrives, to ensure that the respective tugger train transport trolley is positioned precisely at the transfer point. Jesberg: "We have also installed reflectors at certain positions on the transport trolleys, which reflect the light beam emitted by the sensor and thus trigger the impulse for a signal light. If this lamp lights up green, the tugger train driver knows that the trolley is correctly positioned in front of the loading point."
The employee then pushes the rack onto the infeed conveyor - with little effort and in an ergonomically optimal manner. The first rollers of the feed are free-running. The infeed conveyor is started via a muting system and runs in a supportive manner. When the rack is partially on the conveyor, it is automatically transported into the system. The rack is then fed to a corner transfer unit via a second driven roller conveyor. From there, the rack is transported (90° in the longitudinal direction) via a heavy-duty roller conveyor to the bumper removal station. Further loaded racks are lined up one behind the other via the single station control. The maximum storage capacity is four load carriers.
At the removal point, the bumpers are transferred to the assembly worker's area of action. In order to gain access to all bumpers, the inside of the frame is turned manually by the assembly worker. For safety reasons, automatic operation is not possible while the bumpers are being removed. The worker actively requests a rack change by pressing a button, thus initiating the automatic conveying process. Jesberg: "In automatic mode, no employee is allowed to enter the system. In order to create the conditions for personal safety, we have equipped the system with a protective housing on the sides and part of the front sides and with safety light grids in the area of the infeed and at the removal points."
The empty racks are transported via another corner transfer unit and a roller conveyor to the discharge point, where the rack rolls along a heavy-duty gravity roller conveyor until it reaches a manual step barrier. The logistics employees are responsible for removing the empties. To do this, the foot pedal is operated. The empty racks can then be easily pushed from the dispensing area onto the transport trolley.
In the event of a malfunction, the system can be used manually in emergency mode. For this purpose, the conveyor drives are each equipped with a clamping station, which can be used to decouple the drive from the conveyor using a lever mechanism. In addition, the lifting unit in the corner transfer unit can also be raised and lowered manually using a lever. Tread plates between the roller conveyors ensure that the system is easy to walk on. With all these technical features, AMI was able to fully meet the requirements of those responsible at VW for uninterrupted operation of the assembly line.

View from the unloading side of the rear and front bumper assembly area on the assembly line to the automatic
AMI conveyor system
Clear requirements profile defined
The strategic goal of Happyshops managing directors Frank Noack and Robert Letsch to grow more strongly internationally and the increasing demand for products from the Happyshops portfolio, but above all the shortage of staff and its impact on shipping quality, quickly made it clear that automated intralogistics would play a key role here.
The online mail order company commissioned AMI Förder- und Lagertechnik GmbH to implement this requirement profile. "The decision in favor of AMI," says Noack, "was based on the positive experience we had with the planning and implementation of a conveyor system in the shipping department a few years ago. At the time, we were impressed by the technical expertise from planning to commissioning as well as the partnership-based cooperation. And so we also sought direct contact with AMI for the new project.
For the solution provider, the intralogistics project to be implemented was based on the general requirements for increased shipping performance and greater efficiency in the entire intralogistics process.
Another aspect that is currently being discussed intensively in many sectors of industry and commerce had to be incorporated into the planning and design of automated intralogistics. We are talking about the shortage of skilled workers and staff in general. Noack: "With our location in Merseburg, we are right in the middle of the logistics region of Leipzig, Halle and Bad Hersfeld. As a result, we can hardly find any skilled workers or personnel with lower qualifications who meet the requirements for the activities in the shipping areas".
Despite intensive training, it happened time and again that employees working at the packing stations were unsure of the correct postage and the right label sticker for the respective consignment, sometimes taking several minutes to decide.
For Sven Jesberg (photo, center), sales technician at AMI Förder- und Lagertechnik GmbH, it quickly became clear "that we could only achieve our goal here with automated intralogistics that took this particular personnel problem into account, networked the respective subsystems with each other and controlled the entire intralogistics system including all processes via our Logistics Solutions software".
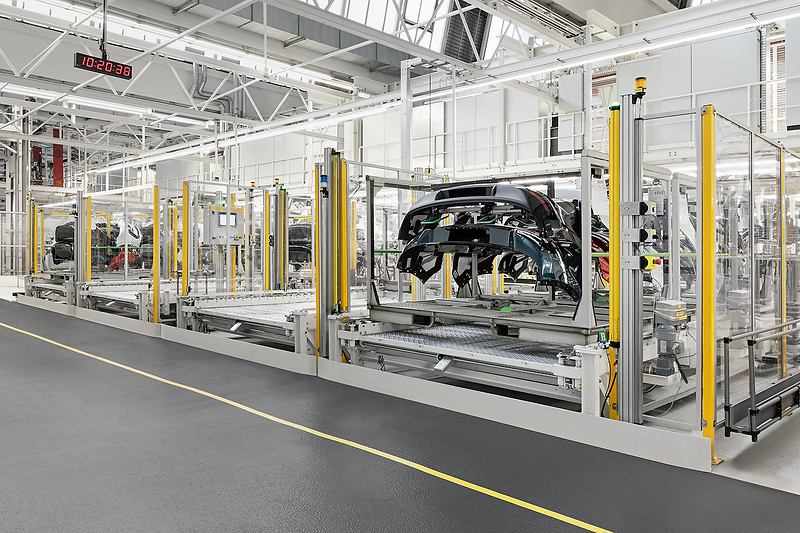
Loading and unloading point for the bumper frames

The limited space demanded a lot from the AMI designers in order to meet all the requirements placed on the conveyor system
Automatic mode: also a question of sensor technology
The sensors play a key role in ensuring that the assembly line runs smoothly and automatically. The sensors used ensure that the assembly process can run smoothly. In this context, they must detect the bumpers in the racks or determine when the worker has removed all the bumpers from the load carrier. "Only then can the system switch to automatic mode, remove the empty rack and prepare the next load carrier," says Erhardt.
In this way, the sensor system has fulfilled one of the important points in the specifications: The automated feeding and transportation of the bumper transport racks.
The system has been in use since January 2020 and has been running smoothly ever since. Erhardt: "We were able to achieve the goals associated with the investment in terms of reducing the walking distances of the workers and the amount of work involved in changing bumper racks for the logistics employees."
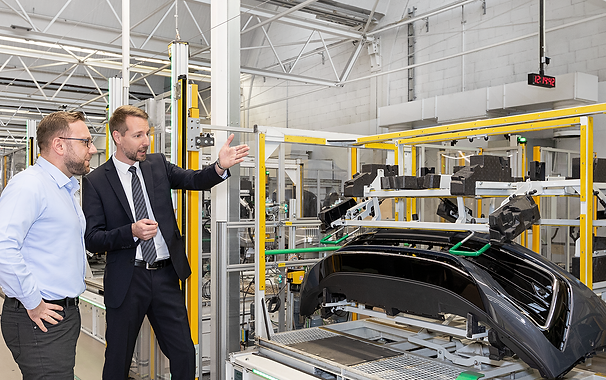
Can look back on a successful project: Denis Erhardt (left), Logistics Planner at the Wolfsburg plant (PWL-P/B) of Volkswagen Aktiengesellschaft, and Sven Jesberg, Sales Manager at AMI Förder- und Lagertechnik GmbH, Luckenbach